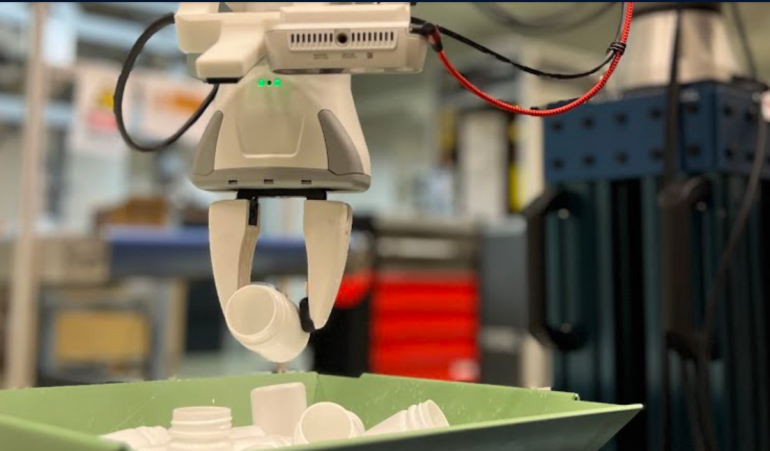
A jumble of miscellaneous objects forms a small mound in front of the IntegrIA Robotics articulated arm. Next to it, in another area, sweets and lollipops, also of various shapes and sizes, are within the robot's grasp. The articulated arm picks up each object one by one and places it in its destination zone.
In the jargon, this is known as "picking". It does not sound like much, except when you consider that for each demonstration, the objects are randomly thrown within the specimen area. And that, of course, the robot is not reprogrammed for each new batch of objects to be moved. The machine therefore operates on its own. It analyses each new situation and then independently makes the best decisions to accomplish its task. This is where artificial intelligence and the expertise of the partners in IntegrIA Robotics, a spin-off of the University of Liège, come into play.
Reinforced learning for autonomous robots
"We have equipped our robotic arm with a camera capable of discerning objects in three dimensions," explains Tom Ewbank, the company's Chief Technology Officer. "But above all, we have developed the artificial intelligence that enables this robot to pick as effectively as possible," explains the research engineer in computer science and robotics.
"Our AI is linked to the vision it has of the pincer's fingers. The prototype first observes the objects placed in front of the camera. It then makes a few movements to get a good feel for the scene. This is called deep reinforcement learning. The system considers the various actions required to complete its task. Its artificial neural network takes an image as input and then works out a plan of action for the robot", he explains on the Wallonia Brussels International stand at Hannover Messe, where he was on hand to promote the quality of his product.
The carrot or the stick
"The system learns, it is a super mathematical model with algorithms for optimising the actions it needs to take," continues Tom Ewbank. "The robot performs various actions during the simulation. And we can, of course, check whether these tasks have been carried out correctly. If they have, we give the system a reward ("+1"). If it does something stupid, for example if it pushes too hard on the objects, then a penalty is applied ("-0.xxx"). The system will try to optimise its operation so that it collects as many rewards as possible. That's how it moves towards optimal operation."
"The potential applications of our AI are many and varied. They include all situations where there is a wide variety of objects to grab, and where it is not cost-effective to redevelop a specific system", explains Audrey Lempereur, Software and AI Engineer at IntegrIA Robotics.
A digital twin as a test bed
"For example, in the case of small production runs or online order management. Our software is adaptable. We can recreate a digital twin of the situation we want to train a system on, and then run it so that it performs well in the situation it will have to deal with," she says.
"Our aim is to offer our customers a software package," says the company's CTO. "But we could also just sell services."
The articulated arm presented at Hannover Messe is a convincing showcase for the young company's expertise. "But we would still like to perfect the system," says Loïc Sacré, the third member of the spin-off. "For example, by making the robot's movements more fluid."
Back in Liège, in their office and laboratory at Sart-Tilman, the team of engineers is keeping its objectives firmly in mind, namely to develop innovative artificial intelligence-based robotic solutions for industry.
Source: Daily Science - Christian Du Brulle